Refrigerated warehouses and cold storage facilities were once considered unattractive investments for several, salient reasons: exceedingly high construction costs, enormous power demands (and the expensive, complex infrastructure to satisfy them) and relatively low demand among end-users. The facilities are still complex and costly, but demand for them shot up quickly during the pandemic and particularly in highly populated sections of the country.
According to the “National Industrial Report” issued by CommercialEdge, there is “currently nearly seven million square feet of new cold storage space under construction across the country and an additional 10 million square feet being planned.” In addition, “cold storage properties accounted for more than $2 billion in sales volume” last year.
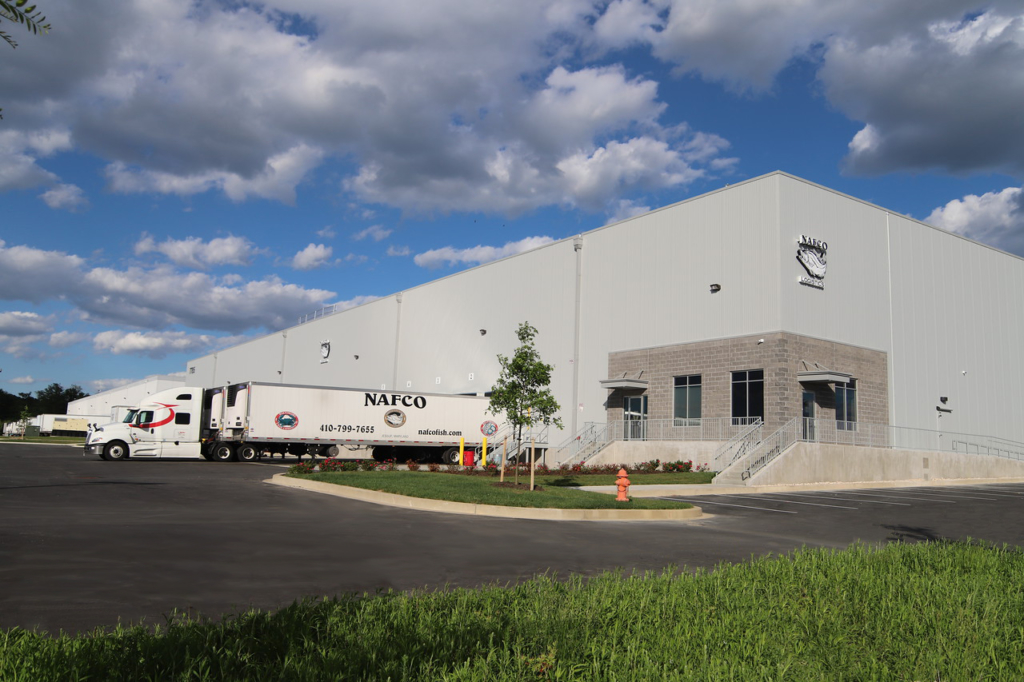
NAFCO Logistics 70,000-square-foot refrigerated seafood distribution center in Jessup features a 61,000-square-foot, -10 degree freezer and 35-degree cold dock. Photo courtesy of Engle Imagery.
Pandemic drives demand for cold storage
A key driver of that demand is food. Over the last two years, consumers have avoided restaurants, cooked homemade meals and subscribed to meal kit services. Consequently, the need for cold storage facilities situated near major population centers skyrocketed.
Consumers have become increasingly health conscious since 2020, which has led to the choice of fresher and sustainable food, including more fruit, vegetables and seafood with short shelf lives. Wary of on-going supply chain issues, large segments of the population are also stocking up on certain food items that can be frozen for an extended period of time, which is placing additional pressure on available cold storage spaces.
Abnormally high demand was also generated by pharmaceutical companies in need of refrigerated space to store raw materials used to produce vaccines and other drugs.
High costs, delayed materials prolong construction
Refrigerated warehouses and cold storage facilities can cost up to $220 per square foot to construct, as compared to the $100 per square foot for typical warehouse product. Construction timelines can be nearly six months longer for a cold storage building, based on its complexity, and retrofitting a dry warehouse into a cold facility rarely saves any time or money as compared to ground-up construction. According to the CommercialEdge report, the worldwide production of magnesium – an essential chemical element used in cold storage construction – may be curtailed due to its harmful impact on the environment, which will elevate prices and increase overall costs.
Cold storage differs from traditional spec warehouse model
Constructing cold storage space on a speculative basis can be tricky due to the varying needs of end-users, suggests Drew Enstice, Director of Business Development for ARCO Design/Build Industrial. He explains that it is difficult, if not impossible, to predict the amount of freezer space, cooler space and room temperature space required by a company, as well as the size and complexity of the production or packaging area needed.
“We’ve seen speculative cold storage in other areas of the country, but very few instances in the Baltimore/DC area so far,” Enstice stated. “We continue to field inquiries from end-users who have outgrown their current space or are looking to move from a 3PL to their own warehouse, but the cost of building their own building is a little more than they’re ready to take on alone. It seems like the need is definitely there and it will be interesting to see what happens locally with cold storage buildings in the next several years.”
Maximizing ROI with ‘fractionalization’
Larry Goodwin, Principal of 1788 Holdings, LLC – a commercial real estate and investment firm based in Bethesda, Maryland – now takes a contrarian view to investing in this asset class after studying the use of smaller cold storage facilities in numerous markets across the country.
“The common belief was to lease a 20,000 to 50,000 square foot cold storage warehouse to one large tenant, similar to the method utilized by traditional dry warehouse buildings, but the scarcity and the daunting investment per square foot to build spaces for smaller users of this product type calls for a different approach, in our view,” explained Goodwin.
He describes a “fractionalization” tactic which entails segmenting a refrigerated space into smaller sections or bays and then leasing these subdivided spaces at a square footage cost significantly higher that what would be charged to a full-building end-user. In order to control the activity by various users within a space, the landlord can also take an “Iron Mountain” approach to inventory stocking and retrieval where they charge additional fees for each pallet or box of inventory coming and going from the space (to account for higher turnover users and scheduling of loading dock usage).
“For instance, restaurants in the immediate area, which previously would need to invest capital to build cold storage facilities within their backrooms – incurring extensive upfront costs and taking away precious space – could now rent out exactly what they need,” said Goodwin. “The multiplier effect of this approach would enable a landlord/investor to realize significantly higher leasing costs. We also see boutique food manufacturing companies as a high probability target audience for this use. By comparison, pharmaceutical companies typically develop build-to-suit cold storage facilities or lease the entire building, so they are not good leasing candidates.”