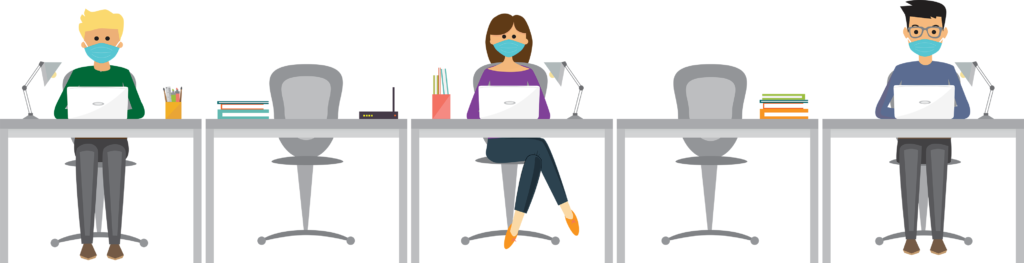
June 4, 2020 – As employers investigate how to safely migrate their staff back from telework, the office of the near future is shaping up to be a curious combination of Star Trek-like technology, medical-grade touches, 1950s office design, 1920s elevator (and possibly bathroom) attendants, and lots and lots of disinfectant.
The tough news about modifying offices and commercial buildings to ease the risks from COVID-19 is that the number of issues to address is seemingly endless. How do you covert a high-density, open-concept office into a personally-protected, socially-distanced workspace? How do you deal with high-rise elevators, daily deliveries, shared bathrooms, employee lunchrooms and those, multi-tenant amenity spaces? And how do you address all those issues in the midst of a sharp economic downturn?
The even tougher news is that you can’t simply avoid those issues and wait for the problem to pass. During an interview on CNN in May, Spencer Levy, Chairman of Americas Research for CBRE, said social distancing and heightened sanitation will be required to bring a percentage of workers back to office buildings while the COVID-19 crisis persists. Commercial buildings likely won’t see more normal occupancy levels for another 12 to 18 months and that return will hinge on “more wellness techniques that are proven during this period,” Levy said.
He compared the current crisis to 9/11. Fearful of returning to urban centers and tall buildings after the 9/11 attacks, workers only began reoccupying those spaces after buildings increased their security.
Faced with a pandemic, “we will see a similar switch…when people increase the wellness in those buildings not just in social distancing but in other systems in the building like HVAC to make people more comfortable,” he said.
The better news is that the public health crisis has triggered widespread innovation in the quest for those solutions; some modifications can be completed inexpensively; and changing social and work norms may make those solutions easier.
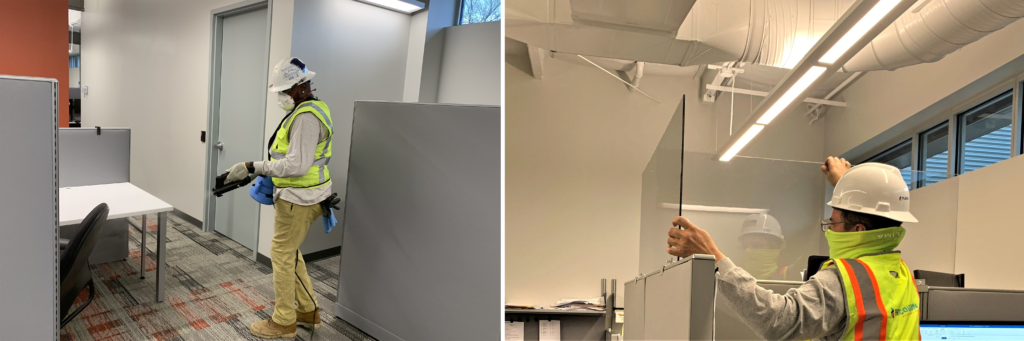
“No one has a playbook for this situation…We are all going to have to do this slowly and figure it out… You certainly don’t want to rush and do major surgery [on your offices]…You don’t want to reconstruct your entire space,” said Chuck Breitenother, Principal at NAI KLNB.
Cushman & Wakefield developed its 6 Feet Office model around the goal of helping companies restart operations safely, quickly and cost efficiently. Some of its core tools are simple floor decals that indicate a six-foot radius around a workstation, one-way (often clockwise) foot paths through workspaces and safe places to stand in an elevator or lobby. Other fundamentals include large, sanitary, disposable desk pads that would be replaced daily and modified building operations that include a central facility for receiving and sanitizing deliveries before allowing them to proceed to office suites.
At Plano-Coudon Construction, building professionals have become aides to planning safer office spaces.
“The CDC and OSHA aren’t regulating what to do in your office or how to be safe… and we’re not pretending to have all the answers. We are just thinking through scenarios and helping clients plan,” said Brett Plano, Co-CEO.
The service grew out of Plano-Coudon’s internal efforts to keep its construction sites safe and functioning back in mid-March when non-essential companies were shuttering.
“Each of our job sites is a different scenario. We could be in a senior living facility, a hospital or an office building that houses other essential workers. So we had to think through how to safely work in all of those environments,” Plano said.
Blair Radney, the head of Plano-Coudon’s Small Projects Division, began using the company’s own office to test possible safeguards, including ways to install plexiglass screens around work areas and a cleaning system that quickly, thoroughly ‘fogs’ entire offices with disinfectant.
Increasingly, clients began requesting assessments of their own workspaces so they could decide on alterations.
To achieve proper distancing and reduce the number of touch surfaces, some companies “may need to break apart some office cubes and move furniture. In some places, they may want to build a hard-wall office or install plexiglass screens,” swinging doors or motion sensors for lights, Radney said.
Such projects aren’t particularly expensive, but potential supply chain challenges mean that clients should decide on renovation plans soon, Radney said. Anticipating a run on plexiglass, Plano-Coudon purchased a $20,000 supply in March.

Modest renovations have been made easier by the fact that “furniture manufacturers, contractors, everyone has taken on the challenge to come up with ways to make the office workable again… It has been inspiring how everyone is adapting so quickly and coming up with solutions,” said Sandy Sawicki, Vice President of Interior Design at JMT Architecture.
The solutions have ranged from simple (but essential) signage to indicate one-way pedestrian paths through office buildings and attachable or freestanding barriers to divide workspaces.
The key to modifying offices to address the evolving COVID-19 situation “is to make space flexible,” she said. “We don’t know what the future will bring so, while we want to distance people now, we don’t want to divide everything into closed offices and leave no open space and no options to change in the future.”
JLL’s “(re) entry” guide to working in the “new normal” points out that preferences among some workers to continue teleworking can help employers achieve lower office densities provided they invest in a little technology. Outfitting meeting rooms with high-speed computer links and large monitors will enable blended teams of onsite and home-based workers to meet and collaborate safely. Employers could further support onsite workers by altering their food service operations, JLL recommended. To avoid midday outings for lunch, employers could encourage staff to bring food to the office or companies could make arrangements with a local restaurant or caterer (maybe a company you previously used for events or business luncheons) to deliver individually packaged lunches.
Simple operational changes – such as running air systems longer and maintaining humidity levels at 40-60 percent – can also reduce risks of spreading the coronavirus.
Some COVID-19 modifications, however, will require bigger investments.
At Bala Consulting Engineers, a COVID-19 Task Force developed a white paper on options to alter building systems to reduce the virus’ spread. Noting that the size of the coronavirus is too small to be caught in filters, the white paper suggested that a combination of two devices – antimicrobial or HEPA filters along with bi-polar ionization technology – could remove coronavirus from a building’s air supply. The ionization technology would cause the aerosolized virus to form charged particles (ions). Those ions would be attracted to dust, smoke, VOCs and other airborne particles that could then be captured in filters.
Bala’s white paper also suggested that placing UVC lamps at strategic locations within the duct system could destroy microorganisms in the airstream. Increasing the flow of outside air through a building, including following the standard or infectious-disease rooms that requires two air changes per hour, could further improve air filtering.

clean pathogens off the clothing and belongings of people who pass through it. Photo courtesy of Healthe.
However, adapting “toilet rooms will be particularly tricky,” said Bruce Votta, Senior Vice President.
Since coronavirus can be transmitted through respiration, touch and fecal-oral transmission, shared restrooms present multiple risks. In addition to maintaining distancing and cleaning surfaces after each use, building operators could lower transmission risks in washrooms by installing Far UVC or UVC lamps, the Bala paper states. Such lights, however, would probably only be practical on completely enclosed toilet rooms.
To reduce the number of touch surfaces in work spaces and reduce contamination sources, product developers, architects and building owners are assessing the benefits of adding a range technologies, including automatic door openers, touchless bathroom fixtures, elevators that can be summoned with a smartphone app and a futuristic device for disinfecting people.
“There is a company that makes a sanitation portal that is straight out of science fiction,” Sawicki said. Shaped like a metal detector, the portal uses ultraviolet light to kill pathogens on the clothes and belongings of people who pass through it. “At first, I thought it was crazy, but apparently it is established technology. It could end up in building lobbies.”
Installing advanced technologies “will be expensive to do, but in the future developers may have to include touchless technologies as a selling feature,” said James Caronna, Principal at NAI KLNB.
In the near term, however, building owners can make improvements through simpler measures, Caronna said. “In one of the office buildings that KLNB occupies, there are one-way up and down staircases now. There is an enter door and an exit door. There are automatic hand sanitizers beside the elevators so you can push the button and immediately wash up. And you see cleaning crews in masks cleaning every touch point in the common areas.”
Visit NAIOP Maryland’s COVID-19 Resources page for more reopening guidelines and information.