Retail e-commerce sales are expected to grow by nearly 14% this year to eclipse the $900 billion mark, a trend that was consistently edging up over the past five years but dramatically accelerated over the past 18 months as a result of the COVID-19 pandemic. With shopping patterns now permanently changed, double-digit growth is expected to continue, according to data from eMarketer, with worldwide e-commerce sales projected to approach $7.4 billion by 2025. Nearly 20% of all retail purchases now come via digital orders.
Across the country, developers of warehouse and industrial product are watching, planning and trying their best to react to the continued surge and changes in requirements requested by end-users, particularly for cold storage facilities. Expected design modifications, the sudden rise in construction materials costs, quantity of dock and loading positions, and other timely topics were discussed at the recent “WARE-HOWS” seminar presented by ARCO Design/Build Industrial.
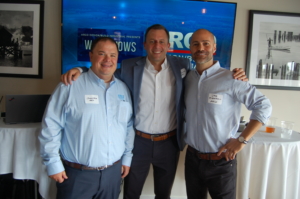
The ARCO Design/Build Industrial team: Aaron Weir, President of Maryland Office; Drew Enstice, Director of Business Development and Joe DiGiorgio, Vice President of ADBI Design Services in ARCO’s New York office.
According to ARCO, the pre-COVID existing supply chain was not built for the dramatic and sustained increase in demand for industrial and warehouse space associated with the near-term post-COVID economic expansion. More simply put by Drew Enstice, ARCO’s Director of Business Development, “we have three kids and go through all kinds of products like crazy, such as diapers, batteries and more. In the past, I would have made a trip to the store for most non-specific items, especially if we needed them quickly. Not anymore. It is just too simple to order online and have the product delivered directly to my house the next day. Now, imagine that scenario being played out day after day in the nearly 130 million households across the United States, and you can see what manufacturers, logistics companies and developers are dealing with on a larger scale.”
Projects face rising construction costs
From an economic perspective, the pandemic has both given and taken away. Construction materials shortages, skyrocketing prices and extended lead times are forcing architects, developers and end-users alike to plan in advance, hoard essential products, anticipate new challenges and become creative problem-solvers.
According to Enstice, every warehouse/industrial construction project consists of “The Big 5” cost elements encompassing sitework, concrete, steel, roofing and fire protection materials, with expenses significantly dominated by sitework. Inflation, coupled with product shortages and an increased demand, have resulted in steel cost increases over the past 10 months with lead times increasing from five to 10 months. Steel joist prices have risen more than 400% in the last year which is adding approximately $11-$12 per square foot to the cost of most warehouse construction projects. Roofing materials pricing have soared 40% and dock equipment and PVC products have increased by half.
“We hope the worst is over and that prices will subside and start to normalize in the near future, but these increases have not impacted the momentum of new construction activity, which speaks to the overall strength of the sector,” Enstice added. “Over the past 18 months or so, the influence on project-wide construction costs has been very significant, causing cost increases per square foot of around 35%-50%.”
100 million sf of cold storage needed
The cold storage sector is expected to grow at a compound annual growth rate of 13.5% through 2028, according to ARCO’s research, with more than 100 million square feet of new space needed over the next five years. The current vacancy rate in this sector nationally is approximately 2%.
The reasons for this growth are many and typically revolve around the storage and delivery of food and pharmaceuticals – two categories undergoing massive disruption. As reported by CNBC and other news outlets, a significant factor in the momentum initiated with Amazon’s decision to begin a two-hour grocery delivery service to its Prime members in 2019. Because cold storage facilities require highly specialized build-out requirements, including floor insulation and significantly higher power supplies, it is more economically feasible to build new, rather than retrofit existing buildings.
“Cold storage facilities are just completely different,” stated Aaron Weir, President of ARCO Design/Build Industrial’s Maryland Office, who presented details on a speculative cold storage project the company is currently building. He explained that the typical facility includes a cold dock freezer section that keeps temperatures between 30 and 40 degrees, freezers with temperatures ranging from zero to 20 degrees below zero and coolers that maintains a 30-to-50-degree environment. Many of these projects also have storage and traditional office space.
“Because end users have such different requirements, most speculative buildings don’t include a complete construction of the flooring or the office areas,” Weir added. “The fire protection systems need to be completely reconfigured because, as you can imagine, traditional water sprinklers are inoperable in below freezing conditions. The average per square footage cost hovers between $150 to $170 and most owners are now underwriting the entire project. We see nothing but continued growth in the future.”
Scarce land, changing user needs alter designs
The surging demand for logistics and last-mile facilities has placed renewed pressure on jurisdictions to change zoning and make decisions regarding priorities for warehouse/industrial product versus commercial office, retail and the booming data center sector. At the same time, the interiors and exteriors of warehouses are changing in response to rapidly-shifting user requirements, including the need for high-density storage, state-of-the-art management systems and automated warehouses.
“In several markets, we are seeing the move to warehouse buildings containing two and three levels in response to the need to achieve required density,” stated Joe DiGiorgio, Vice President of ADBI Design Services who works in ARCO’s New York office. “Other trends are single-story buildings with roof parking, parallel parking structures and stacked truck courts.
“The Multi-story 2.0 warehouse packages contain more auto and van parking, fewer dock positions for inbound product capability and dedicated positions for outbound loading. These designs are occurring in isolated markets across the country but are likely a sign of things to come when dealing with land scarcity and competition for other product uses.”
Across the board, these buildings are growing larger, include 130-foot truck courts, feature up to 40-foot clear ceiling heights (up from 28 feet which was common just 10 years ago) and state-of-the-art automated fulfillment technology and equipment. Sustainability elements, such as green rooftops, are also starting to creep into the newer designs.
With no indication of diminishing demand, this industrial strength is not expected to dissipate in the foreseeable future.